Advantages of cast iron
Durable, versatile, and reliable for industrial use
Cast iron has been a cornerstone in industrial manufacturing for centuries. Its unique properties, such as remarkable strength, effective heat retention, machinability, and resistance to corrosion, continue making it a preferred choice across diverse industries, including commercial vehicles, construction and heavy machinery.
BIRN is specialized in grey and ductile iron castings
As a specialized foundry dedicated to grey and ductile iron castings we ensure precision components tailored to specific industrial requirements. Our many years of experience we guarantee consistent quality, reliability, and performance in critical industrial applications.
Key advantages of cast iron
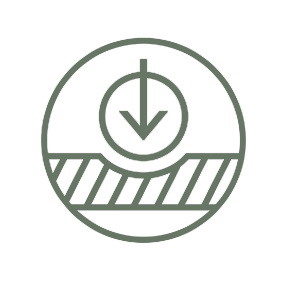
Exceptional durability and strength
Industrial cast iron components are widely known for their resilience under pressure, vibration, and demanding conditions. Cast iron’s robust structure significantly extends component life, reducing downtime and maintenance costs.
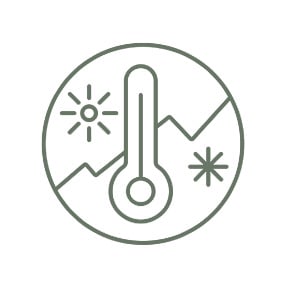
Superior heat retention and thermal stability
Due to excellent thermal conductivity and dimensional stability, cast iron is the ideal choice for heavy-duty applications involving high temperatures, vibrations and humid conditions. Industries frequently utilize cast iron in engine brackets, battery brackets, exhaust manifolds, hydraulic applications, gear housings, gear boxes, water pump housings, where consistent heat distribution is essential.
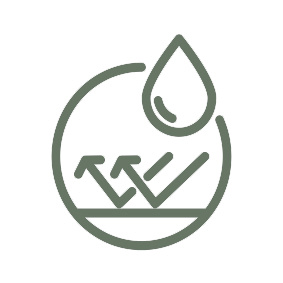
Corrosion resistance
When appropriately coated or surface-treated, cast iron resists rust and corrosion even in harsh environments. Protective surface treatment enhance its lifespan, reducing the frequency and cost of maintenance. Furthermore, cast iron is superior in corrosion resistance over steel, as the surface will hamper deep corrosion once the surface has corroded.
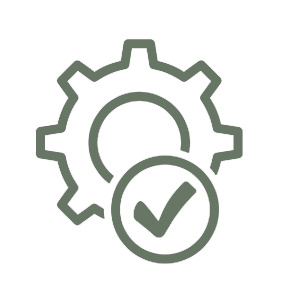
Machinability and cost-effectiveness
Cast iron provides excellent machinability, allowing complex shapes. Transitioning from forged or fabricated components to cast iron often simplifies manufacturing, reducing both material costs and production times and allow more uniform geometrical shapes. Also, most often the CO2 footprint will be reduced due to less energy consumption and utilization of recycled material.
Industrial applications of cast iron
Thanks to its distinct advantages, cast iron serves crucial roles in several industries:
-
Commercial vehicles:
Cast iron are extensively used in the automotive sector for components such as engine blocks, brake discs, crankshafts, transmissions, engine brackets, battery brackets, mud guard brackets, cabin brackets, spring brackets, and various attachment brackets and structural components. -
Construction equipment and material handling:
The construction industry relies on cast iron for products like structural components, motor brackets, engine brackets, battery brackets, cabin brackets, suspension brackets, gear covers, wheel forks, and various brackets and covers. -
Mobile and industry hydraulics:
The mobile and industry hydraulics segment greatly benefits from cast iron for components such as pumps and motor housings, swash plates, pistons, gear housings, pump and covers, in- and outlet valves and covers. -
Transmission and machine elements:
In the realm of transmission and machine elements, cast iron is favored for manufacturing components such as gear- and transmission housings, covers, bearing housings and caps, bearing covers and other machine components. -
Defence:
Cast iron plays a crucial role in the production of defence and military equipment parts and munition parts such as mortar bodies.
Maximizing cast iron’s benefits
To fully leverage cast iron’s strengths:
- Select the correct type (grey iron or ductile iron) to suit specific applications.
- Apply protective surface treatments or coatings for corrosion resistance.
- Regularly inspect and maintain cast iron components to ensure extended reliability.
Cast iron continues to play a vital role in industry due to its exceptional durability, versatility, thermal stability, and cost-efficiency. Selecting appropriate cast iron types, employing protective treatments, and optimizing designs allows industries to benefit from its reliability and proven performance, ensuring operational excellence across numerous industrial applications.
Types of cast iron and their differences
Ductile (nodular) cast iron vs. grey cast iron
Ductile iron, also called nodular cast iron or SG iron, offers improved flexibility and toughness compared to grey cast iron, making it ideal for high-stress parts such as engine and battery brackets, brake parts, cabin and suspension brackets, chassis brackets, connection rods, reaction rod brackets and various structural brackets. The ductility increases the mechanical properties especially with respect to elongation properties.
Cast iron vs. stainless steel
Cast iron provides several benefits compared to steel, such as excellent vibration dampening, cost advantages, and simpler production processes while steel deliver superior tensile strength suitable for high-performance applications.
Switching from steel fabrication or forging processes to cast iron casting streamlines manufacturing, reduces costs, and ensures consistent quality and performance. Choosing casting processes over traditional welding and forging can yield higher reliability and manufacturing efficiency.
Cast iron vs aluminium components
In many applications, utilization of cast iron mecanical properties will be an advantage over aluminium components. Due to higher strengt and for ductile iron also it’s ductility can reduce the size of the components. Further, the environment footprint will be reduced using cast iron as it is almost solely based on recycled materials.
Properties of cast iron
Properties | Grey cast iron | Ductile iron |
Graphite form | Flake | Nodular |
Strength | Moderate | High |
Ductility | Low | High |
Wear resistance | Good | Moderate |
Machinability | Excellent | Moderate |
Vibration damping | High | Moderate |
CONTACT
Manufacturers around the world trust us to bring out the best in their most critical parts – and we are ready to earn your trust.
Peter Frost Jepsen, Chief Sales Officer (CSO)
Let's talk