Recycling of casting sand
Casting sand is recycled instead of ending up as landfill
We use large amounts of sand in the casting process. All sand is reused several times. To ensure good sand quality, two per cent of the casting sand is replaced with new sand on a daily basis. However, the sand that is replaced does not end up as landfill but will instead be recycled for building and construction projects.
Sand is an important element in the casting processes at BIRN as it is used in the custom-designed moulds for the casting facility. Sand is a great choice for casting, as it is able to withstand the extreme heat from the molten iron. Therefore, at BIRN we supply more than 21.4 tonnes of fresh sand and 38.4 tonnes of core sand every day. In this way, the casting facility renews 2% of its casting sand every gram, while 98% is recycled in the casting process
98% recycled sand
Only two per cent of the daily quantity of sand used by BIRN is new sand - the rest is recycled from previous casting processes.
We recycle the casting sand several times ourselves in our own casting production but at some stage it will eventually reach the point at which it can no longer be used in our own processes. However, it can be used in the building and construction industry - for example, in building foundations and roads - so therefore we send it on for reuse there.
As the recycled sand may contain residual material from the casting process, a special permit is always required in order for it to be used for building and construction purposes. However, BIRN is more than happy to assist with the administrative process so that it does not become a burden for the recipient.
- The sand is typically covered with asphalt, concrete or similar, and the site where it is used will be registered as containing casting sand, including all sand test results. This requires a permit but we are familiar with the application process, so therefore we often assist recipients of our used casting sand with this, explains BIRN CTO, Lars Jørgensen.
Article
Waste sand utilised in new collaboration
BIRN launched an exciting partnership in 2024 with Y-MatTec, a local high-strength concrete manufacturer, to recycle surplus sand.
Read the article hereRead about all of BIRN Group’s different initiatives within the field of sustainability.
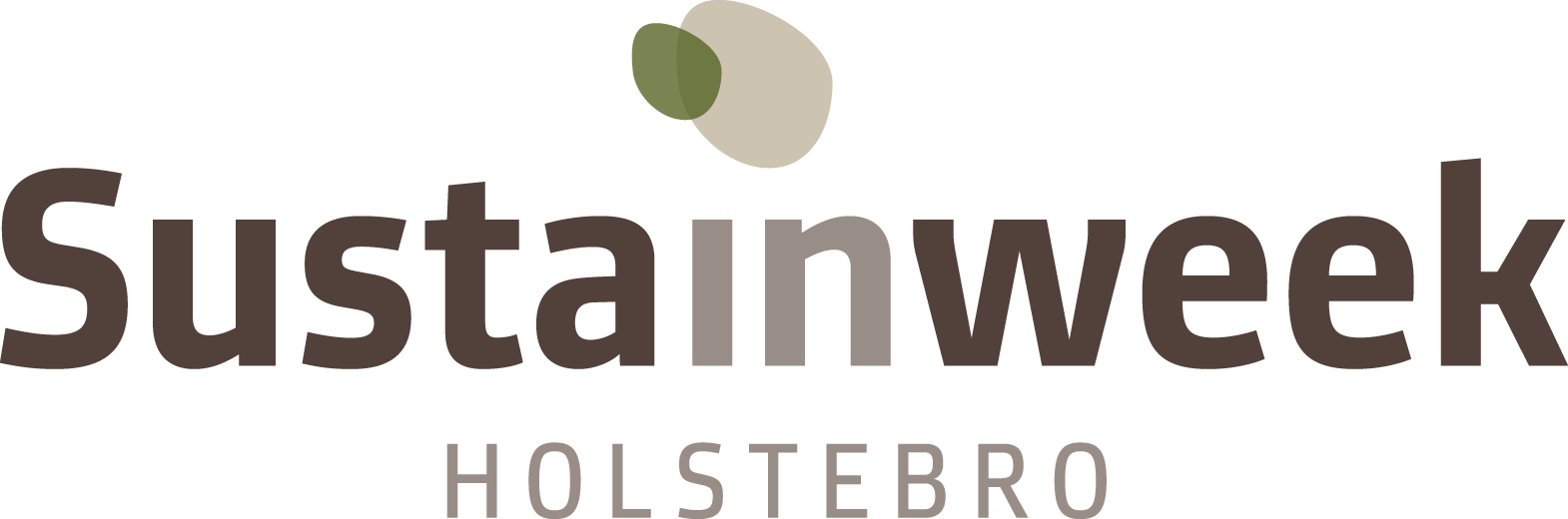
Turning the tide on sand consumption
Sustain Week was successfully held in the first week of September 2023, with strong participation from BIRN. We participated with our case on the recycling of excess foundry sand.
The process of sand in our production
Fresh sand for casting moulds
BIRN receives 21.4 tonnes of fresh/raw sand every day, which is used for the casting moulds.
Core sand for core production
The sand used to produce cores is washed, purified and dried sand. BIRN receives 38.4 tonnes here on a daily basis.
Up to 98% of the sand is reused - 2% of the sand is renewed with new sand, core sand, clay and coal on an ongoing basis.
Fresh sand is mixed for casting moulds
The raw sand is mixed with clay, coal dust and water. After that, it’s ready to be pressed into casting moulds.
Casting moulds made of sand can withstand cast iron of up to approximately 1,500 degrees Celsius.
Core sand is mixed into cores
The core sand is mixed with bentonite, binder and hardener. After this, the sand is pressed into cores that form the cavities in the cast iron units.
The cores are blackened in order to protect the cores against the high temperatures and to give the iron units a smooth inner surface that form the cavities in the cast iron units.
Cast iron is poured into the sand moulds
The 1,500-degrees Celsius hot cast iron is poured into the sand moulds.
This happens in large DISA machines, which can take up to approximately 1,300 units per hour depending on the size of the units.
Cast iron units are shaken free of sand
When the casting process is complete and the sand moulds with the pre-cast units have cooled, the sand is shaken free from the units.
Surplus sand
Only 2% of the sand used in production cannot be recycled due to wear and tear.
This sand is separated, loaded into containers and has water applied so that it does not form dust. Every day, 83 tonnes of surplus sand is taken away from the factory. This is equivalent to 20,000 tonnes per year.
Recycling surplus sand
Surplus sand from production at BIRN is suitable for buildings
- for example, for foundations when establishing roads, stable buildings or similar.
Contact
Can your company use surplus sand from BIRN?
If so, then we would be very happy to hear from you.
Lars Jørgensen, CTO
Contact us