Iron castings
High-volume iron casting with automatic moulding technology
BIRN stands as a fully equipped casting facility with an annual production volume of approx. 45,000 tons across five fully automatic DISAMATIC moulding lines. Our expertise spans more than 125 years, delivering the benefits of cast iron to diverse key industrial sectors worldwide.
Our customers rely on us to provide competitive cast iron components manufactured to precise specifications, ensuring consistent performance and quality in every delivery.
Technical iron casting capabilities
We specialize in high-quality ductile iron and grey iron castings within the weight range of 200g to 40 kg, both with and without cores, in medium to high volumes. Our vertically integrated facility ensures complete quality control throughout the entire production process.
Our casting capabilities:
- Unit weights from 200g to 40kg
- Mould sizes: 480x600mm, 600x775mm, and 700x950mm
- Five fully automatic DISAMATIC vertical moulding lines
- Annual casting capacity of 45,000 tons
- Core manufacturing
- Automated pattern changing systems for quick production changeovers
Unit weights from 200g to 40kg
Mould sizes:
480x600 mm
600x775 mm
700x950 mm
Five Disamatic vertical moulding machines
Casting capacity of 45,000 tons a year
AI project
The casting process
Your iron casting designs are produced on our five vertical DISAMATIC Moulding Machines using advanced pattern equipment. Our flexible production setup allows us to serve a wide range of industries through our comprehensive range of DISAMATIC molding systems with automatic core and filter insertion.
We continually invest in new technology to follow market developments and meet evolving customer requirements. An example to this is our AI-project we made in cooperation with pour-tech AB to optimize dosing of molten iron from casting machines into molds. The dosing process plays a crucial role in the heating process, quality and energy consumption.
Read more about the AI-projectAdvanced Core Manufacturing
At BIRN, we specialize in producing cast iron components with complex core structures that form the internal cavities of the parts. Our advanced core shop is equipped with automated core blowing machines that deliver high dimensional accuracy and intricate designs.
We offer extensive in-house cold box core production using core shooters, with capacities ranging from 100g up to approx. 20kg. Our production lines include manual, semi-automated, and fully automated setups. Only water-based coatings are used, and cores are dried using both heat and microwave technologies. Croning cores are sourced from trusted sub-suppliers to ensure consistent quality.
Project planning and lead times
Our production planning systems enable us to optimize scheduling and minimize lead times. For new projects, we work closely with customers from the design phase through prototyping to series production, ensuring efficient time-to-market.
Quality control
Strong focus on quality control ensuring the highest level of quality
Our metallurgical laboratory continuously monitors material quality, allowing us to maintain precise control over the mechanical and chemical properties of every casting batch.
After the iron casting process is complete, our comprehensive quality control system includes metallurgical testing, dimensional verification, material certification, and both destructive and non-destructive testing methods. Each batch undergoes rigorous inspection to ensure compliance with customer specifications and relevant industry standards.
Sustainability in our castings
Our iron casting processes are designed with sustainability in mind. We implement circular business models through extensive recycling of scrap metal and casting sand, while our energy management systems continuously work to reduce our environmental footprint.
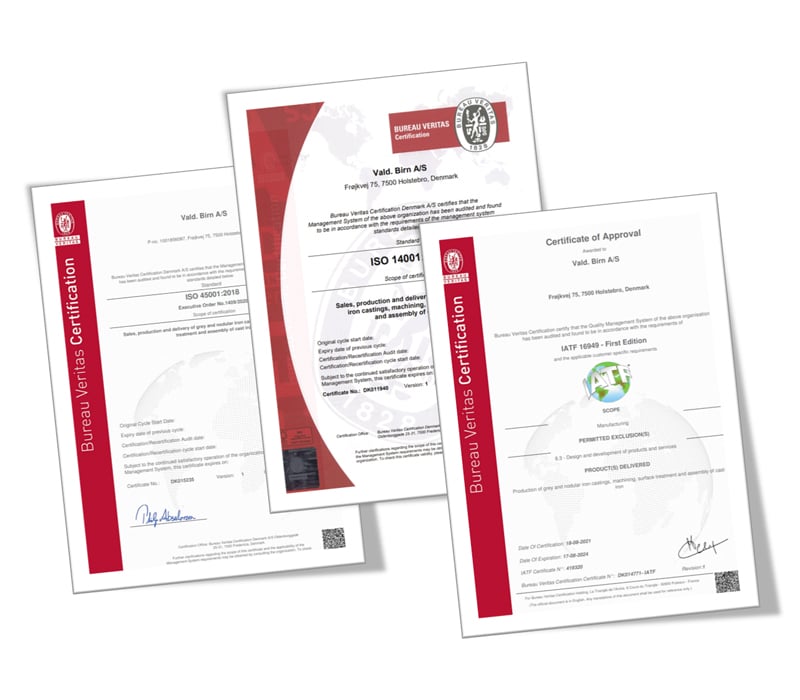
Certifications
BIRN maintains the highest quality standards through certification programs that ensure consistent quality and performance. Our certifications demonstrate our commitment to quality, environmental responsibility, and workplace safety.
Download our key certifications:
IAFT 16949 - Automotive quality management system
ISO 14001 - Environmental management system
ISO 45001 - Occupational health and safety management
Related services
Design
Our in-house enginering team are always ready to assist you in optimising your early-stage designs to secure optimal production.
Machining
Our automated solutions in machining secure competitive production of your ready-to-assemble parts.
Surface Treatment
We protect your components surfaces by offering cataphoresis (ED) primer and powder paint coating applied in our new in-house paint facility.
CONTACT
Manufactures around the world trust us to bring out the best in their most critical parts – and we are ready to earn your trust.
Peter Frost Jepsen, Chief Sales Officer (CSO)
Let's talk