Circular Business Model
Circular mindset
The BIRN Group’s business model is based on a circular economy mindset. For us, it has long been common sense to consider how we use and consume the planet’s resources. We upcycle waste materials, recycle our own materials in closed circuits and develop products with a long life that can be reused indefinitely. BIRN prepares ongoing life cycle analyses precisely to map the flow of materials and waste.
However, the manufacture and treatment of cast iron also produce a number of waste products. Our waste management has long been based on the waste hierarchy, but, with a circular approach, we must be even more conscious of how we create added value and waste fewer resources. What other industries categorise as waste may be a resource for us, and vice versa.
Examples of recycling
98% of the sand from the casting process at BIRN in Holstebro is recycled
93% of the materials in BIRN’s cast iron are recycled material such as scrap
58% of the space heat at BIRN in Holstebro comes from recycled heat from production
20% of the smelting iron at BIRN in Holstebro comes from recycled shavings and wire from used car tyres
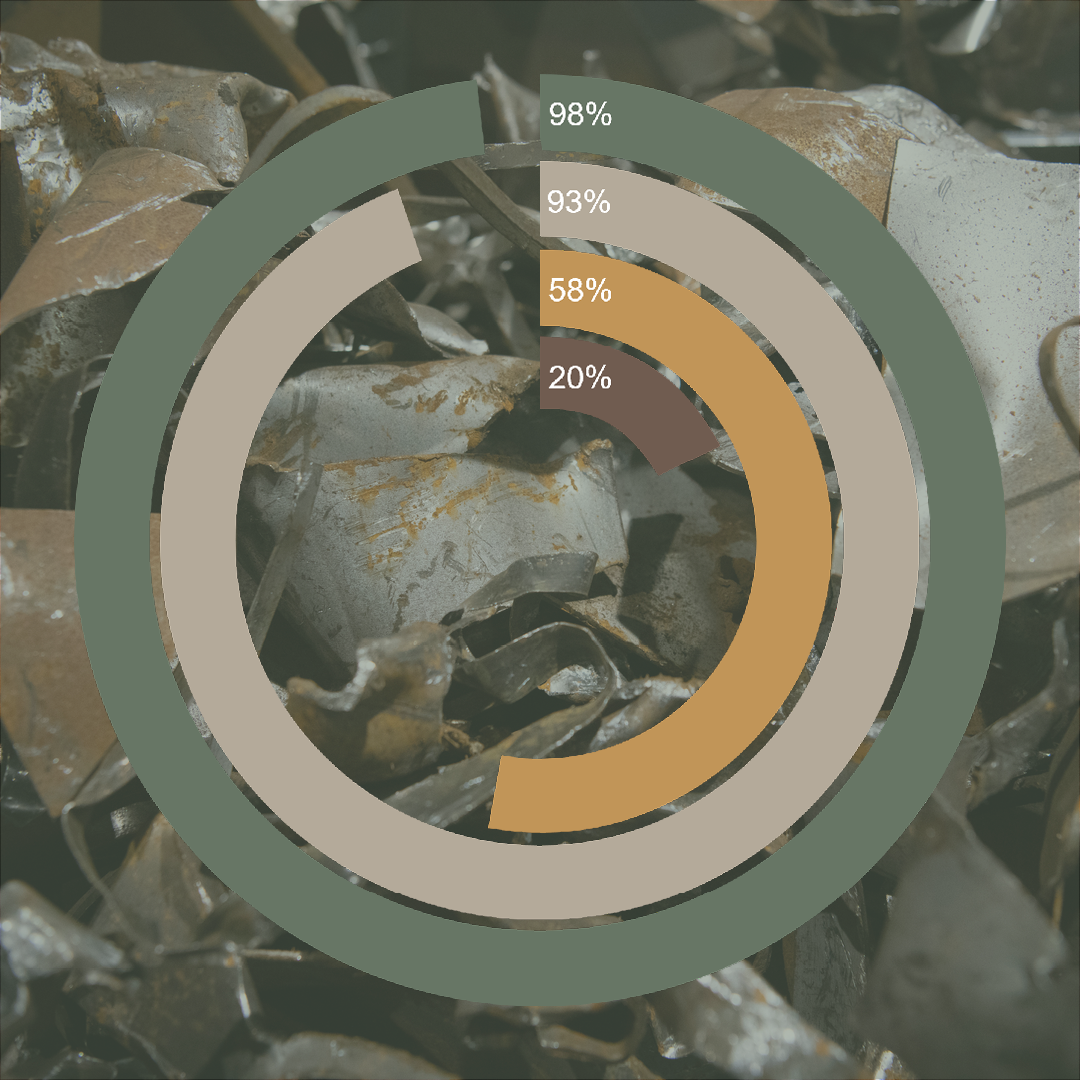
Recycling of scrap
Virtually all the scrap that BIRN purchases comes from Denmark. This means, among other things, that the transport of steel scrap from supplier to our foundry is minimized and that we use as little pig iron as possible.
Recycling of casting sand
Sand is an important element in the casting processes at BIRN as it is used in the custom-designed moulds for the casting facility. Sand is a great choice for casting, as it is able to withstand the extreme heat from the molten iron.
Recycling of scrap
Steel scrap is the main component in BIRN's cast iron production. In fact, BIRN's cast iron consists of as much as 93 percent recycled material, which comes from e.g . cars, trucks and washing machines to steel from construction and industrial production. Virtually all the scrap that BIRN purchases comes from Denmark. This means, among other things, that the transport of steel scrap from supplier to our foundry is minimized and that we use as little pig iron as possible.
Read more about recycling of scrapRecycling of casting sand
Sand is an important element in the casting processes at BIRN as it is used in the custom-designed moulds for the casting facility. Sand is a great choice for casting, as it is able to withstand the extreme heat from the molten iron. Therefore, at BIRN we supply more than 21.4 tonnes of fresh sand and 38.4 tonnes of core sand every day. In this way, the casting facility renews 2% of its casting sand every gram, while 98% is recycled in the casting process
Read more about recycling of casting sandDistribution of raw material consumption
The composition of materials in cast iron consists of both virgin and recycled raw materials. Recycled raw materials include steel scrap, machining shavings and foundry returns from the casting process. Virgin raw materials include pig iron and alloy materials.
Emissions and energy
As one of the largest foundry groups in Northern Europe, and thus an emitter of greenhouse gases, we are committed to continuing our work to reduce emissions connected with our operations.
Read moreContact
Sustainability is an important driver in ensuring the future success of our business. Do you want to know how we work with sustainability?
Emil Husted Brodersen, Group Sustainability Manager
Let's talk