On the lookout for new and better scrap sources
On the lookout for new and better scrap sources
90,000 tonnes of iron are melted at BIRN in Holstebro each year. 93 per cent of this comes from recycled material such as scrap steel from old cars, discarded refrigerators and tyre wire from used car tyres. But even more scrap is needed. So the foundry group is constantly on the lookout for new and better sources of scrap, business models and partnerships throughout the entire value chain.
In 2024, BIRN in Holstebro took part in Sustain Week, an initiative of ErhvervsForum Holstebro, for the second year running. The event brings together companies, researchers and world-leading specialists to discover and develop innovative sustainable solutions in a number of specific cases. One of the aims of participating in 2024 was to identify alternative materials and technologies that can increase the company’s recycling of iron and steel scrap, and ensure that the scrap purchased has the lowest possible climate impact.
“We are very pleased with our participation in Sustain Week and the valuable insights we have gained. It gave us the opportunity to engage in many good conversations about future collaborations with companies that have surplus scrap, while increasing our awareness of the alternative scrap sources available,” says Lars Jørgensen, Group COO at BIRN Group.
BIRN in Holstebro has annual consumption of around 90,000 cubic metres – equivalent to the consumption of about 2,400 people. Water is an essential resource for cooling equipment used for cast iron production and for other processes in the factory’s daily operations.
BIRN has had its own well since the 1970s, to secure the water supply at the factory. This is operated in the same way as municipal waterworks, with controls and approvals. Water is pumped up, filtered and purified before it is used in production or as drinking water.
Sustain Week is a forum where companies can meet in a more informal setting. This element, in particular, led to many good conversations with current and potential suppliers about the requirements and expectations they are encountering from customers and business partners, especially with regard to sustainability, Lars Jørgensen explains:
“We are considering all options in our quest to lower our carbon footprint. With scrap being one of our
absolute most important materials, it is extremely relevant for us to consider where the scrap we use comes from and its climate footprint. Following on from our participation in Sustain Week, we have therefore conducted a supplier assessment to help us choose suppliers who are committed to sustainability.
Alternative skrotkilder
One of the successful recycling solutions that BIRN in Holstebro already uses is tyre wire briquettes, which primarily consist of metal wire from end-of-life car tyres and cast iron shavings. These briquettes make a key contribution to the company’s recycling efforts and support the goal of increasing the use of alternative scrap sources:
"Tyre wire briquettes are a textbook example of what we need even more of: alternative sources and materials for scrap – and perhaps from new places we cannot even imagine. In addition to supporting the circular economy, we have also found that briquettes have become an economic advantage, while meeting the rising demand we are seeing for more sustainable solutions,” notes Lars Jørgensen.
One of the other opportunities that BIRN in Holstebro is exploring is participation in take-back schemes. Under these schemes manufacturers of products, such as trucks – to whom BIRN supplies cast iron components – enter into agreements with their customers to take back end-of-life products, with the aim of recycling as much of the materials as possible. Take-back schemes support the circular economy by ensuring that resources are optimally utilised and reintroduced into the production chain, reducing the need for new raw materials.
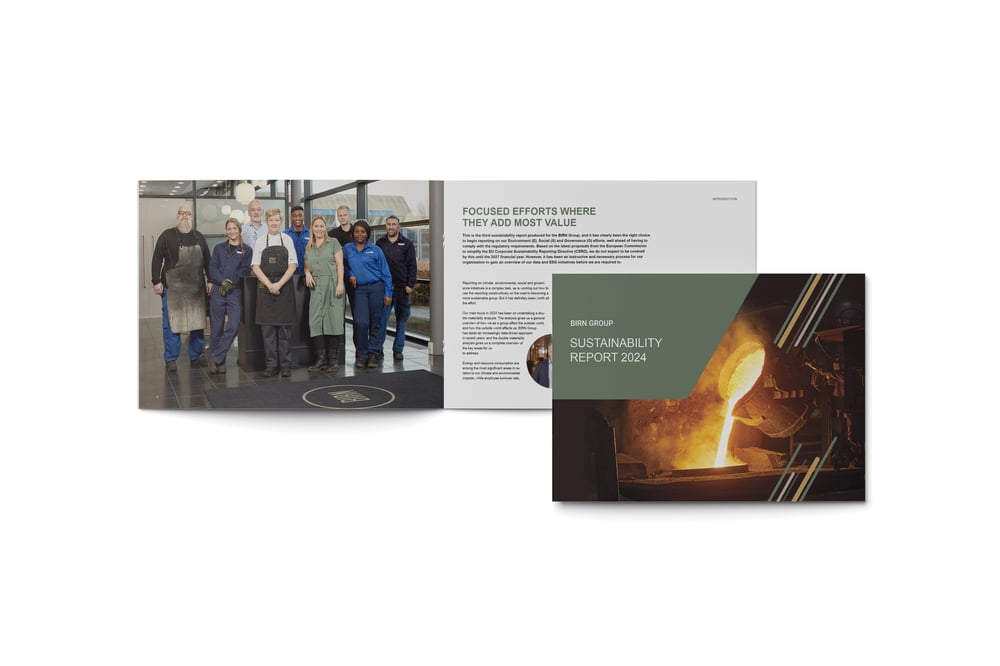